Hi, my name is Lisa Dinwoodie. I'm an applications engineer for Texas Instruments' Low Power Controllers and Converters Group. This presentation is a quick tutorial on the different types of flyback converters and the terminology used to describe them. The intent is not to go into design detail. But after this presentation, you should have a basic understanding of the different terms used to describe flyback converters, such as discontinuous, continuous, quasi-resonant, and valley switching. So let's get started. Let's begin with a quick review of the basics. What is a flyback converter? A flyback converter is a simple switch-mode power supply. Flybacks can be used to generate a DC output from either an AC or DC input. Flybacks are designed in such a way that the power from the input is transferred to the output during the off-time of the primary switch. They are generally used in the low- to mid- power range, usually less than 100 watts. There are several advantages to the flyback. This topology has a low parts count consisting of an input capacitor, a primary site switch, usually a MOSFET, a coupled inductor called the flyback transformer, an output rectifier, and an output capacitor to create a flyback converter. Thanks to the transformer, input to output isolation is possible. Careful design of the turns ratio between the primary and the secondary enable the output to be higher or lower than the input and also enables support of a wide input voltage range. A flyback can support multiple outputs by adding more windings to the transformer. The flyback converter uses a single magnetic, although commonly referred to as a transformer actually behaves as a coupled inductor. This transformer combines the functions of energy storage, energy transfer, and isolation, so the need for a separate LC filter on each output is eliminated. This greatly reduces the overall cost of flybacks as compared to other topologies. All flybacks have the same operating principle. When the MOSFET turns on, energy from the input source it's stored in the transformer, specifically, the gap in the transformer. This is much like filling a bucket from a well. Think of the source as a well and the transformer is the bucket. Because of the transformer winding scheme, noted by the dot polarity markings on schematic, the output diode is reverse-biased and off during the on-time of the MOSFET. When enough energy is stored in the transformer, the MOSFET switch is turned off, the bucket stops filling, and the diode now connects and energy from the transformer is delivered to the load. It is important to note that the MOSFET and the diode should never conduct at the same time. The bucket never empties while it's being filled. When the MOSFET turns on, this is referred to as the on-time of the converter. The input voltage is applied to the primary side of the transformer. The primary side current ramps up. During this time, the secondary side diode is reverse-biased, and the voltage applied to the diode is equal to the output voltage plus the reflected input voltage. The output capacitor supplies the load current during the on-time. When the MOSFET turns off, the current in the transformer transfers to the secondary and flows through the diode that is now forward-biased, replenishing the output capacitor and supplying the load. The secondary side current ramps down as the transformer core demagnetizes. During this MOSFET off-time, the primary side is considered an open circuit. The voltage applied to the MOSFET is equal to the input voltage plus the reflected output voltage. Note that the drain to source and the diode voltage equations shown here are simplified and do not account for the additional voltage stresses from circuit parasitics. A flyback is operating in Discontinuous Conduction Mode, or DCM, when the power stage is designed in such a way as to allow the transformer to completely demagnetize during each switching cycle. The simplest form of a DCM flyback is designed with a fixed switching frequency and modulates the peak current to support the load demands. At the start of the switch period, the on-time begins and the primary side current ramps up from zero. At the end of the on-time, the primary current collapses back to zero, and current flows to the secondary windings. It begins at its peak proportional to the turns ratio and ramps down to zero, completely demagnetizing the transformer during every switching cycle. After the demagnetizing time, there is a delay before the primary side switch turns on again to start the next switching cycle. This delay is referred to as dead-time or resonant time. During this portion of the switching period, neither the diode nor the MOSFET is conducting. This dead-time, where the transformer is completely demagnetized and no current is being conducted, is why this operating mode is called discontinuous, or DCM. During this dead-time, a resonant ring is generated by the interaction between the primary inductance of the transformer and the parasitic capacitance at the switch node. A converter in deep discontinuous mode can have a dead-time long enough for the resonant ringing to dampen completely, at which point the drain to source voltage will have settled to be equal to the input voltage. The high frequency ringing when the MOSFET is turned off is the result of the resonance formed between the leakage inductance and the switch node parasitic capacitance. Because the leakage inductance is much smaller than the primary inductance, this ringing will be at a much higher frequency than the resonant ring during the dead-time. This high-frequency ringing will add to the drain to source voltage stress, and it should be included in the voltage range of the MOSFET. For a fixed input voltage, increasing load demand results in longer on-time, allowing the peak current to rise higher. The amplitude of the peak current is modulated and the converter is operating in the AM-- or Amplitude Modulation-- range. The secondary side peak current will proportionally rise to a higher peak when the diode begins to conduct. And the dead-time portion of the switching period will decrease to maintain the constant switching frequency. The advantages of DCM flyback are that there are no reverse recovery losses in the output rectifier, because it's able to ramp down to zero amps during every switching cycle. The primary inductance value is lowest out of all the flybacks, which may result in a smaller transformer. A DCM flyback is inherently more stable, because it doesn't have a right-half-plane zero in its transfer function. DCM flybacks do have the disadvantage of very large ripple currents, which may require large EMI filters. Fixed frequency DCM flybacks have higher losses because they can turn off the switch when the drain to source voltage may be relatively high. It can be ringing higher than the input voltage at the moment of turn-off. This could contribute a considerable hit to efficiency, as the switching losses are proportional to the square of this voltage. Texas Instruments has a selection of controllers that support discontinuous flybacks, such as the UC2842 family of devices, the UCC28C40 family, and the UCC2800 family, and the LM5021. Valley switching is a specialized form of discontinuous conduction mode and requires a controller that is specifically designed to detect when the resonant ring during the dead-time is at a low point before turning the MOSFET on to start the next switching cycle, minimizing switching losses. In order to maintain the required average output power, the controller will modulate the switching frequency by skipping one or more valleys from one cycle to the next. Controllers that modulate the frequency to meet the average load demand every cycle are operating in FM, or frequency modulation, mode. This is sometimes also called frequency foldback, because as the load demand is decreased, the switching frequency is also decreased, or folded back. Valley switching can occur at any resonant valley during the dead-time, as long as it's large enough for the control to detect. The switching waveforms may appear to dither as the controller adjusts it's dead-time in its search for the nearest valley. Valley switch flybacks have all the advantages of traditional DCM flybacks with the added bonus of lower switching losses due to consistently turning the MOSFET off when the drain to source voltage is at a low value. This also helps to reduce the turn-on current spike at the current sense resistor. The dithering produced by valley skipping helps to reduce EMI. Unfortunately, valley skipping will result in higher output voltage ripple. Also valley switching is ineffective if the converter is operating in deep discontinuous mode, as the controller will not have enough of a signal to detect a valley. TI controllers that support Valley switching are the UCC28610, the UCC28720 and 722, the UCC28700 family, the UCC28704, and the UCC28710 family, UCC28730, and the UCC28740, along with the UCC28910 and 11. These controllers offer a variety of other features, such as cable compensation, thermal protection, primary side regulation, low power standby, et cetera. The details are provided in each data sheet found on the TI website. Quasi-resonant mode, or QR, may also be referred to as critical conduction mode or transition mode. Quasi-resonant operation is a specific valley switching operating mode of DCM where the switching occurs on the very first and deepest resonant valley. QR delivers the maximum amount of power by adjusting both the peak current and the switching frequency to turn the MOSFET on at the first resonant valley for minimal losses. QR controllers operate in AM and FM mode at the same time to meet the demands of energy transfer. QR controllers will decrease the switching frequency as the load increases. This is just the opposite of frequency foldback mentioned earlier. Most valley switching controllers, such as the ones mentioned previously, can operate in quasi-resonant mode, but only at the specific operating point of maximum load and minimum input voltage when designed accordingly. This limited QR range of operation is due to the control method used in the valley switching controllers, where only the frequency is modulated-- not both the frequency and the peak current, like in dedicated QR controllers. Because QR mode converters switch at the lowest drain to source voltage, they achieve the lowest possible switching losses and have high efficiency over the entire operating range. Because this is a soft switching converter, only small EMI filters are needed. QR converters are difficult to compensate due to the wide peak current and switching frequency ranges. Considerable phase margin is required to maintain stability over the entire operating range. The UCC28600 and the LM5023 are specifically designed for QR operation. But, as mentioned earlier, valley switching controllers can be used in a design that achieves QR mode at the minimum line and maximum load operating point. Let's talk about CCM now. CCM refers to continuous conduction mode. A continuous current is always flowing in the transformer during each switching cycle. When the MOSFET is turned on, the primary current ramps up. But it doesn't start from zero amps as in DCM, or discontinuous conduction mode. In CCM, the current ramps from an offset that is due to residual energy that is continuously maintained in the transformer. When the switches turned off, energy is transferred across the secondary and the transformer demagnetizes, resulting in the secondary side current ramping down. But it does not ramp all the way to zero amps. Residual energy is maintained in the transformer. The next switching cycle begins before the current is completely depleted. As shown, the current waveform on both the primary and the secondary is trapezoidal in shape. This is sometimes referred to as a ramp on a step. Note that there is no dead-time in CCM. Current is always being conducted somewhere in the transformer. But also note that despite continuously conducting current, the MOSFET and the diode do not conduct at the same time. As the load demand decreases, the store of residual energy, the step portion of the wave form, decreases. CCM flyback transformers are designed based upon the ripple current, or ramp portion, of the wave form, which is considerably less than the ripples seen in DCM flybacks. Controllers specifically designed for valley switching will not operate in CCM, as there is no resonant ring available and the transformer is not allowed to fully demagnetize. The advantages of continuous conduction mode, or CCM, are the small ripple and RMS currents, which result in lower capacitor losses. These lower currents also help lower conduction and turn-off losses when compared to DCM flybacks. Lower peak currents means smaller filter components. The most noted disadvantage of CCM flybacks is the presence of a right-half-plane zero in the power stage transfer function. This limits the bandwidth of the control loop and will impact the converter's dynamic response. Also, CCM flybacks require a larger inductance, which may require a larger magnetic component. The UCC28630 controller family is specifically designed for CCM operation, but there is nothing to limit using generic current mode controllers, such as the LM5021, the UC2842, the UCC28C40, or the UCC2800 device families in a CCM design. The operating point just on the cusp of DCM and CCM is referred to as the boundary condition. This is the operating point where the MOSFET is turned on at the precise moment when the transformer has demagnetized so there is no resonant ring. But at the same time, there is no energy stored in the transformer. There is no step or residual current stored. Converters that can operate in both CCM, as shown, will transfer through the boundary condition when it passes to DCM operating. CCM converters will pass through into DCM at very light loads. Because CCM has a more limited bandwidth, converters that allow passing from DCM to CCM should be compensated for CCM. Converters that require resonant valley detection to switch do not allow CCM, and so will not operate at the boundary condition. Now that the basic flyback mode terminology has been explained, you may be wondering which converter would be best for your application. Output power level and peak switching currents may help determine the optimum operating mode. Specific features, such as operating temperature range, turn-on and off thresholds, programmable soft start, low power mode, primary side regulation, high voltage startup, cable compensation, among others, will determine the controller most suited for the application Texas Instruments has a wealth of information available from our Power Supply Design Seminar series which is available to you. And this includes many topics specific for flybacks. Please visit ti.com/psds for more information. I hope this presentation was useful and helped to clarify the basic terminology used to describe flyback modes of operation. For more information on flyback converter design or any of the data sheets that the controllers mentioned, please consult the TI website. Thank you for your time.
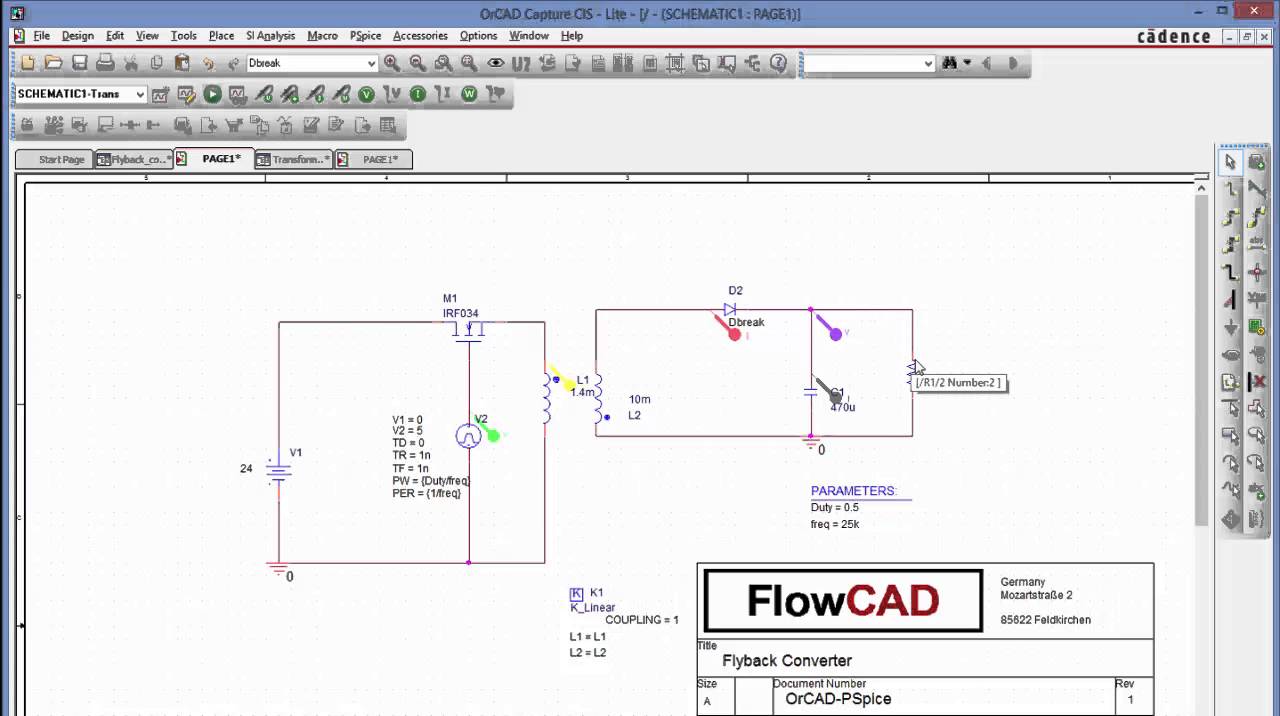
Description
Valley switching, discontinuous, continuous, or quasi-resonant? This presentation demystifies the alphabet-soup nomenclature used to describe the different types of Flyback converters.
Additional information
Flyback Converter Design In Pspice Tutorial
Lecture notes KFUEIT Document Linear circuit analysis GIKI Power Electronics Basic electric circuits notes EE-110 Electric Drives Prof P Gopakumar Scribd Electronics EE-355 EE-211 Power systems Video Tutorial Simulation EE-231 Flyback inverter Digital Logic Design Notes EE-434 Experimental work PSPICE Computational Electromagnetic Theory Grid. PSpice simulates the circuit, and calculates its electrical characteristics. If we need a graphical output, PSpice can transfer its data to the Probe program for graphing purposes. Also Pspice is a simulation program that models the behavior of a circuit. And Pspice is a Product of the OrCAD Corporation and the student version we are using is. Circuitry Operation of Flyback Converter. If we see the basic single output flyback design like the image below we will identify the basic main components which are required to build one. A basic flyback converter requires a switch, which can be a FET or transistor, a Transformer, an output Diode, a Capacitor. The main thing is the transformer.
Comments are closed.